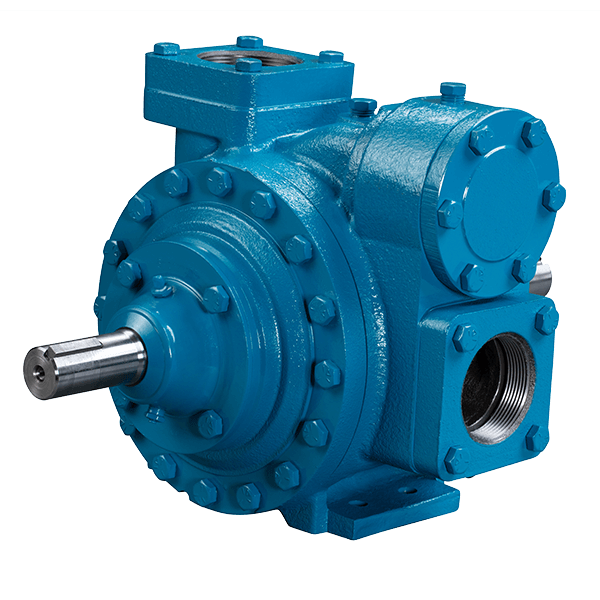
Vane Pumps Explained
Understanding Design, Operation, and Versatile Applications
Introduction to Vane Pumps
Vane pumps are a type of positive displacement pump that use vanes mounted to an eccentrically placed rotor to move fluid. As the rotor turns, the vanes slide in and out of slots, creating expanding and contracting volumes between the vanes, rotor, and housing (cam ring). They are known for their ability to handle low to medium viscosity fluids, good dry-running capabilities (for some types), and consistent flow output. Vane pumps are found in various hydraulic, automotive, and industrial applications.
Working Principle: Sweeping Action
Vane pumps operate through a simple yet effective mechanism:
- Eccentric Rotor: A slotted rotor is positioned eccentrically within a circular or elliptical cam ring (housing).
- Sliding/Flexible Vanes: Vanes fit into the rotor slots. As the rotor turns, centrifugal force, springs, or hydraulic pressure push the vanes outwards to maintain contact with the inner surface of the cam ring.
- Chamber Formation: The space between adjacent vanes, the rotor, and the cam ring forms chambers. Due to the eccentricity, these chambers increase in volume on the suction side, drawing fluid in.
- Fluid Transfer & Discharge: As the rotor continues to turn, the chambers decrease in volume on the discharge side, forcing the trapped fluid out of the pump.
The close tolerance between vanes, rotor, and cam ring ensures efficient pumping action.
Key Components of a Vane Pump
Rotor
A cylindrical component, typically slotted, driven by the shaft and mounted eccentrically within the cam ring.
Vanes
Flat, rectangular (sliding vane) or flexible elements that fit into the rotor slots and move radially to seal against the cam ring.
Cam Ring / Housing
The stationary outer ring or housing with a precisely machined internal contour against which the vanes slide or flex.
Shaft
Transmits power from the driver (e.g., electric motor) to the rotor.
End Plates (Side Plates)
Seal the sides of the rotor and vanes, forming the pumping chambers along with the cam ring.
Seals & Bearings
Shaft seals prevent leakage, and bearings support the shaft for smooth rotation.
Main Types of Vane Pumps
Based on Vane Design:
- Unbalanced: Rotor is eccentric to a circular cam ring, leading to side loading on the shaft. Simpler design.
- Balanced: Elliptical cam ring with two inlet and two outlet ports opposite each other. Hydraulic forces on the rotor are balanced, reducing bearing load and wear. More complex.
Other Classifications:
Drive Methods
Vane pumps are typically driven by:
Electric Motors
Most common drive method in industrial settings.
Internal Combustion Engines
For mobile applications or where electricity is unavailable.
Hydraulic Motors
In hydraulic systems where the pump is part of a larger hydraulic circuit.
Advantages & Disadvantages
Advantages
- Handle low to medium viscosity fluids well.
- Can handle some entrained gases or vapors.
- Good dry-running capability (especially flexible vane or some sliding vane designs).
- Low pulsation and smooth flow compared to some other PD pumps.
- Compensate for wear (sliding vanes extend further).
- Variable displacement versions offer flow control.
- Good suction lift capabilities.
- Relatively compact for their output.
Disadvantages
- Generally not suitable for highly viscous fluids or large solids (except specific designs).
- Sliding vanes are susceptible to wear from abrasive particles.
- More complex than gear pumps, with more moving parts.
- Lower pressure capabilities compared to piston or plunger pumps.
- Flexible vanes have temperature and chemical compatibility limitations.
- Can be sensitive to system contamination.
Common Materials of Construction
Housing/Cam Ring
- Cast Iron
- Ductile Iron
- Bronze
- Stainless Steel
- Hardened Tool Steels
Rotor & End Plates
- Carbon Steel
- Hardened Steel
- Stainless Steel
- Ductile Iron
Vanes
- Carbon/Graphite
- Hardened Steel
- Bronze
- PEEK, Torlon® (engineered plastics)
- Elastomers (Nitrile, EPDM, Viton® for flexible vanes)
Typical Applications
Vane pumps are utilized in a diverse range of applications:
Key Selection Considerations
- Fluid Properties: Viscosity, lubricity, temperature, chemical compatibility, presence of abrasives or gases.
- Operating Conditions: Required flow rate, discharge pressure, suction conditions (lift or head).
- Duty Cycle: Continuous or intermittent operation.
- Dry Running Capability: Is it required? Affects vane material and type.
- Noise Level: Balanced vane pumps are generally quieter.
- Space Constraints: Vane pumps are relatively compact.
- Flow Control Needs: Fixed or variable displacement.
- Material Compatibility: Critical for vanes, housing, and seals.
- Maintenance Requirements and Cost.
Vane Pump vs. Gear & Centrifugal Pumps
Feature | Vane Pump | Gear Pump | Centrifugal Pump |
---|---|---|---|
Principle | Positive Displacement | Positive Displacement | Dynamic |
Viscosity Handling | Low to Medium | Medium to High | Low (typically) |
Flow Output | Smooth, Low Pulsation | Some Pulsation | Continuous, Non-Pulsating |
Dry Run Capability | Good (some types) | Poor (generally) | Very Poor (requires priming) |
Complexity | Moderate | Simple | Simple |
Efficient Fluid Handling with Vane Technology
Vane pumps offer a unique and effective solution for a variety of fluid transfer needs, particularly for low to medium viscosity liquids. Their ability to compensate for wear, provide smooth flow, and handle some dry running conditions (in certain designs) makes them valuable in many industrial and mobile applications. Understanding the differences between sliding vane and flexible vane types, as well as balanced and unbalanced designs, is key to selecting the optimal pump for specific performance and longevity requirements.