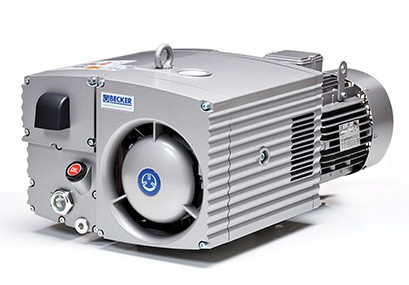
Vacuum Pumps Explained
Creating and Maintaining Vacuums Across Industries
Introduction to Vacuum Pumps
A vacuum pump is a device that removes gas molecules from a sealed volume to leave behind a partial vacuum. The primary goal is to create an environment with a pressure lower than the surrounding atmospheric pressure. Vacuum technology is indispensable in a vast range of scientific research, industrial processes, and everyday applications, from manufacturing semiconductors to food packaging and medical devices. Different pump types are designed to operate effectively across various vacuum pressure ranges.
Working Principle Categories
Vacuum pumps can be broadly categorized by their mechanism of gas removal:
Gas Transfer Pumps
These pumps move gas molecules from the vacuum chamber to an exhaust. They operate by either trapping and compressing gas (positive displacement) or by imparting momentum to gas molecules (kinetic/momentum transfer).
- Positive Displacement: Rotary Vane, Piston, Diaphragm, Lobe, Screw, Scroll.
- Kinetic/Momentum Transfer: Turbomolecular, Diffusion.
Gas Binding/Capture Pumps (Entrapment)
These pumps remove gas molecules by condensing them on cold surfaces or by chemically or physically binding them to internal surfaces. They do not exhaust gas; they trap it within the pump.
- Examples: Cryopumps, Ion Pumps (Sputter Ion, Getter Ion), Non-Evaporable Getter (NEG) Pumps, Titanium Sublimation Pumps (TSP).
General Key Components
(Varies significantly by pump type)
Overview of Common Vacuum Pump Types
Positive Displacement Pumps
Kinetic / Momentum Transfer Pumps
Entrapment / Gas Binding Pumps
Key Vacuum Terminology
Vacuum Level (Pressure Ranges):
- Rough Vacuum: Atmospheric to ~1 mbar (or Torr)
- Medium Vacuum: ~1 mbar to 10-3 mbar
- High Vacuum (HV): ~10-3 mbar to 10-7 mbar
- Ultra-High Vacuum (UHV): Below 10-7 mbar
Pumping Speed (S):
Volume of gas removed per unit time (e.g., L/s, m³/hr) at a given inlet pressure. Not constant; varies with pressure.
Throughput (Q):
Quantity of gas (pressure × volume) pumped per unit time (e.g., mbar·L/s). Q = S × P.
Ultimate Pressure (Pult):
The lowest pressure a pump can achieve in a sealed, clean, and empty system. Also known as base pressure.
Gas Load:
The total amount of gas entering the vacuum system per unit time from all sources (process gas, leaks, outgassing).
Typical Applications by Vacuum Level
Rough & Medium Vacuum:
Food packaging, vacuum forming, medical suction, freeze drying, mechanical handling, backing for HV/UHV pumps, vacuum distillation, filtration.
High Vacuum (HV):
Semiconductor manufacturing (sputtering, etching), thin-film coating, electron microscopy, mass spectrometry, leak detection, space simulation chambers, vacuum furnaces.
Ultra-High Vacuum (UHV):
Surface science research, particle accelerators, fusion research, molecular beam epitaxy, advanced materials research where extremely clean environments are needed.
Key Selection Considerations
- Required Ultimate Pressure: Determines the type or combination of pumps needed.
- Pumping Speed & Throughput: Must handle the system’s gas load to reach and maintain the target pressure within a desired time.
- Gas Composition: Corrosive, reactive, particulate-laden, or condensable gases require specific pump types and materials.
- Process Compatibility: Oil-sealed vs. dry pumps (oil backstreaming concerns).
- Operating Costs: Power consumption, maintenance, consumables (oil, cryogens).
- Vibration and Noise Sensitivity of the application.
- Space and Utility Requirements.
- System Volume and Outgassing Rates.
- Need for Backing Pumps: Many HV/UHV pumps (e.g., turbos, diffusion, cryos) require a rough/medium vacuum pump to exhaust to.
- Budget: Initial purchase cost versus long-term operational costs.
Enabling Modern Science and Technology
Vacuum pumps are indispensable tools that create the controlled low-pressure environments necessary for a vast array of scientific breakthroughs and industrial innovations. From enabling the production of microchips to facilitating research into the fundamental nature of matter, their role is often unseen but absolutely critical. The diverse range of pump technologies available allows engineers and scientists to select the optimal solution for achieving the specific vacuum conditions required by their unique applications.