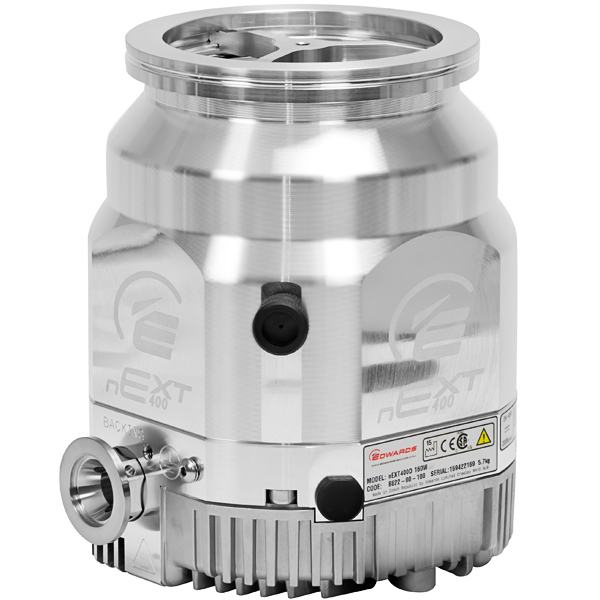
Turbo Molecular Pumps Explained
Achieving High and Ultra-High Vacuum with Kinetic Power
Introduction to Turbomolecular Pumps (TMPs)
Turbomolecular pumps (TMPs) are a type of kinetic vacuum pump used to obtain and maintain high vacuum (HV) and ultra-high vacuum (UHV) conditions. They operate on the principle of momentum transfer, where rapidly rotating turbine-like blades impart momentum to gas molecules, directing them from the vacuum chamber towards a backing pump. TMPs are essential in many advanced scientific and industrial applications requiring very low pressures and clean vacuum environments.
Working Principle: Momentum Transfer
TMPs utilize high-speed rotors to pump gas:
- High-Speed Rotor: A multi-stage rotor assembly, consisting of angled turbine blades, spins at very high speeds (tens of thousands of RPM).
- Gas Molecule Collision: Gas molecules entering the pump from the vacuum chamber collide with the rapidly moving rotor blades.
- Momentum Imparted: During these collisions, momentum is transferred from the blades to the gas molecules, giving them a velocity component in the direction of the pump’s exhaust (foreline).
- Stator Redirection: Stationary stator blades, angled opposite to the rotor blades, redirect the gas molecules towards the next rotor stage, preventing backflow and further compressing the gas.
- Multi-Stage Compression: This process is repeated through multiple rotor/stator stages, progressively increasing the gas pressure towards the exhaust.
- Backing Pump Requirement: TMPs cannot exhaust directly to atmospheric pressure. They require a backing pump (e.g., rotary vane, scroll, or diaphragm pump) to reduce the pressure at the TMP’s outlet (foreline pressure) to a level where the TMP can operate efficiently.
Simplified Turbo Stages Action
Key Components of a Turbomolecular Pump
Rotor Assembly
A series of precisely machined discs with angled blades (turbine stages) mounted on a central shaft.
Stator Assembly
Stationary rings with angled blades positioned between the rotor stages to direct gas flow and improve compression.
Drive Motor
A high-frequency electric motor (often integrated) that spins the rotor at very high speeds (e.g., 20,000 to 90,000+ RPM).
Bearings
Support the high-speed rotor. Types include precision ceramic ball bearings, magnetic levitation (Maglev) bearings, or hybrid systems.
Housing (Casing)
Encloses the rotor and stator assembly, forming the vacuum boundary with inlet and outlet flanges.
Controller Unit
Manages motor speed, power supply, monitors operating parameters (speed, temperature, vacuum), and provides interlocks.
Drag Stages (in Compound Pumps)
Some TMPs incorporate additional pumping stages (e.g., Holweck, Siegbahn) at the exhaust end to improve compression ratio and allow operation against higher foreline pressures, sometimes reducing backing pump requirements.
Main Types/Variations of TMPs
Based on Bearing Technology:
Based on Pumping Stages:
Key Performance Parameters
- Pumping Speed (S – L/s): Volume of gas pumped per unit time at the inlet flange. Varies for different gases.
- Compression Ratio (K): Ratio of outlet (foreline) pressure to inlet pressure for a given gas. Higher for heavy gases, lower for light gases (e.g., H2, He).
- Ultimate Pressure (Pult – mbar or Torr): Lowest pressure the TMP can achieve, limited by gas backflow and outgassing.
- Maximum Throughput (Qmax – mbar·L/s): Maximum quantity of gas the pump can handle.
- Foreline Pressure Tolerance: Maximum outlet pressure against which the TMP can operate effectively.
- Startup Time: Time required for the pump to reach its operational speed and performance.
- Vibration Level: Important for sensitive applications like electron microscopy. Maglev pumps offer the lowest vibration.
- Gas Type Influence: Performance (speed, compression) differs significantly for light vs. heavy gases.
Advantages & Disadvantages
Advantages
- Achieves High Vacuum (HV) and Ultra-High Vacuum (UHV) levels.
- Provides a clean, hydrocarbon-free vacuum (especially Maglev and dry-backed systems).
- High pumping speeds for most gases.
- Relatively fast startup times compared to some other HV/UHV pumps.
- Can operate in any orientation.
- Long operational life, especially for Maglev types.
- Compound TMPs can handle higher foreline pressures.
Disadvantages
- Requires a backing pump to exhaust to (cannot discharge to atmosphere).
- Susceptible to damage from sudden air inrush, particulates, or mechanical shock.
- Lower compression ratio for light gases (H2, He) compared to heavy gases.
- High initial cost, especially for Maglev and large pumps.
- Bearings (ceramic ball type) are wear items and require eventual replacement.
- Controller unit adds complexity and cost.
- Can generate vibrations (ball bearing types), potentially affecting sensitive equipment.
Common Materials
Rotor & Stator Blades
- High-strength Aluminum Alloys
- Titanium Alloys (for higher stress or specific applications)
Housing & Flanges
- Aluminum Alloys
- Stainless Steel (for UHV compatibility or corrosive gas handling)
Typical Applications
TMPs are crucial in advanced technology and research:
Key Selection Considerations
- Target Ultimate Pressure & Operating Pressure Range.
- Required Pumping Speed for different gas species.
- Gas Load from the system (process gas, outgassing, leaks).
- Type of Gases to be Pumped: Corrosive, reactive, light vs. heavy gases.
- Backing Pump Compatibility: Required foreline pressure, dry vs. oil-sealed backing.
- Vibration Sensitivity of the Application: Dictates bearing type (Maglev preferred for low vibration).
- Cleanliness Requirements: Hydrocarbon-free for UHV applications.
- Orientation and Space Constraints.
- Frequency of Venting/Cycling.
- Budget (Initial and Operational Costs including power and maintenance).
- Control and Interfacing Requirements.
Operational Aspects
Backing Pump Requirements
TMPs always need a backing pump to reduce the pressure at their exhaust to a suitable level (typically in the rough or medium vacuum range). The choice of backing pump (e.g., dry scroll, diaphragm, or oil-sealed rotary vane) depends on the TMP type and application cleanliness requirements.
Venting & Startup/Shutdown
Proper venting procedures (usually with dry nitrogen or argon) are crucial to prevent contamination and mechanical stress during shutdown. Startup involves bringing the TMP to operational speed after the backing pump has achieved sufficient foreline vacuum.
Bakeout Compatibility
For UHV applications, the TMP and system components may need to be “baked out” (heated to high temperatures) to desorb gases from internal surfaces. The TMP must be compatible with these bakeout temperatures, or isolated during the process.
Key to Advancing Science & Technology
Turbomolecular pumps are indispensable for achieving the high and ultra-high vacuum environments required by many leading-edge scientific research fields and advanced industrial manufacturing processes. Their ability to provide clean, reliable vacuum with high pumping speeds makes them a critical enabling technology. While requiring careful system design, particularly concerning backing pumps and operational procedures, the performance of TMPs is often unparalleled for demanding HV/UHV applications.