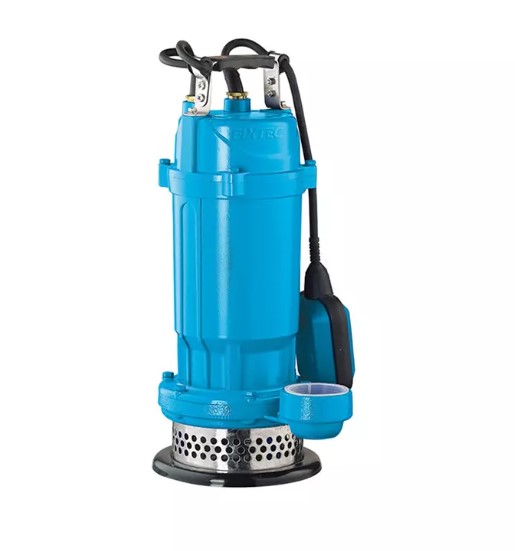
Submersible Pumps Explained
Delivering Fluids from Depths with Efficiency
Introduction to Submersible Pumps
A submersible pump is a device that has a hermetically sealed motor close-coupled to the pump body. The entire assembly is submerged in the fluid to be pumped. This design offers significant advantages, primarily preventing pump cavitation (a common problem with above-ground pumps trying to pull fluid from a depth) and providing efficient motor cooling by the surrounding fluid. Submersible pumps are widely used for well water, drainage, sewage, irrigation, and various industrial applications.
Working Principle: Pushing Fluid Upwards
Most submersible pumps are multistage centrifugal pumps:
- Submerged Operation: The pump and motor unit are fully immersed in the fluid.
- Motor Drives Impellers: The sealed electric motor drives a series of impellers mounted on a common shaft.
- Fluid Pressurization: Fluid enters the pump through an intake screen. Each impeller-diffuser stage adds pressure (head) to the fluid. The fluid is pushed, not pulled, upwards.
- Discharge: The pressurized fluid is discharged through a pipe connected to the pump outlet, typically rising to the surface or the desired delivery point.
- Motor Cooling: The surrounding fluid cools the motor, allowing for continuous operation.
By being submerged, the pump operates under positive inlet pressure, effectively eliminating suction lift limitations and cavitation issues related to suction.
Simplified Submersible Pump in a Well
Key Components of a Submersible Pump
Pump End (Wet End)
Contains impellers, diffusers, suction intake/screen, and discharge head. This is where fluid pressurization occurs.
Electric Motor
Hermetically sealed and close-coupled to the pump. Can be oil-filled or water-filled for cooling and lubrication.
Seals (Mechanical Seals)
Prevent water or pumped fluid from entering the motor housing and protect bearings.
Power Cable
Specially designed waterproof cable that supplies power to the submerged motor.
Casing / Housing
Encloses the pump and motor, made from corrosion-resistant materials.
Intake Screen
Prevents larger debris from entering the pump impellers.
Main Types of Submersible Pumps
Well Pumps / Borehole Pumps
Long, slender design for deep wells and boreholes. Typically multistage centrifugal to achieve high head. Used for water supply.
Sump Pumps
Used to remove accumulated water from sumps or basements.
- Effluent Pumps: Handle small solids.
- Sewage Pumps: Handle larger solids and wastewater.
- Grinder Pumps: Macerate sewage solids into a fine slurry.
Fountain / Pond / Aquarium Pumps
Smaller, often lower-power pumps designed for water circulation, aeration, and decorative features.
Slurry Submersible Pumps
Heavy-duty construction with agitators and robust impellers to handle abrasive slurries in mining, dredging, or industrial wastewater.
Dewatering Pumps (Utility Pumps)
Portable pumps used for removing water from construction sites, flooded areas, or utility vaults.
Advantages & Disadvantages
Advantages
- Self-Priming: Being submerged, they are inherently primed.
- No Cavitation Risk (due to suction lift): Positive inlet pressure prevents cavitation.
- Higher Efficiency: Fluid is pushed, not lifted by suction, often leading to better efficiency for deep applications.
- Motor Cooling: Surrounding fluid cools the motor effectively.
- Quieter Operation: Submersion dampens noise.
- Space Saving: No need for a pump house or above-ground installation space for the pump itself.
- Can handle greater depths than surface-mounted pumps.
Disadvantages
- Maintenance & Repair: Access can be difficult and costly as the pump needs to be pulled out.
- Seal Failure Risk: Hermetic seals are critical; failure can lead to motor damage.
- Potential for Corrosion: Continuous submersion requires corrosion-resistant materials.
- Electrical Safety: Waterproof cable and connections are paramount.
- Cost: Can be more expensive initially than some surface pumps, especially for specialized materials or deep well applications.
- Difficult to Inspect: Visual inspection of operation is not possible.
Common Materials of Construction
Casing & Pump End
- Stainless Steel (common for well pumps, corrosion resistance)
- Cast Iron (sump pumps, some industrial)
- Bronze (seawater applications)
- Engineered Plastics/Composites (smaller, lighter duty, or corrosive apps)
- Hardened Alloys (for slurry pumps)
Impellers & Diffusers
- Stainless Steel
- Noryl®, Lexan® (engineered thermoplastics)
- Bronze
- Cast Iron
- Hardened Iron/Alloys (for abrasive service)
Motor Housing & Seals
- Motor Housing: Stainless Steel, Coated Carbon Steel.
- Seals: Mechanical seals with faces like Carbon/Ceramic, Silicon Carbide, Tungsten Carbide; various elastomers (NBR, Viton®).
Typical Applications
Submersible pumps are essential in numerous scenarios:
Key Selection Considerations
- Required Flow Rate (Q) and Total Dynamic Head (TDH).
- Well/Sump Diameter and Depth: Pump must physically fit and be able to lift fluid from the required depth.
- Fluid Type: Clean water, wastewater, slurry, chemicals; consider corrosiveness, abrasiveness, temperature, presence of solids.
- Solids Handling Capability: Impeller type (e.g., vortex, grinder) if solids are present.
- Power Supply Available: Voltage, phase, frequency. Length and size of power cable.
- NPSH: While less of a concern due to positive submergence, it’s still relevant for pump design.
- Materials of Construction: For fluid compatibility and lifespan.
- Motor Protection Features: Overload, dry run, temperature sensors.
- Duty Cycle: Continuous or intermittent operation.
- Installation Requirements & Accessibility for Maintenance.
Installation & Priming Highlights
Installation
- Carefully lower the pump into the well/sump using appropriate lifting equipment and cable/pipe.
- Ensure power cable is properly secured and protected.
- Verify correct electrical connections and motor rotation (for 3-phase).
- Install check valves in the discharge line as needed to prevent backflow and protect the pump.
- Secure the pump if necessary to prevent movement.
Priming
- Generally Not Required: A major advantage of submersible pumps is that they are inherently primed by being submerged in the fluid. The pump casing and suction are always filled.
- Initial Fill (Some Cases): Some specific designs or very deep installations might require the riser pipe to be filled initially to reduce start-up load, but the pump itself is primed by submersion.
Efficiently Moving Fluids from Below
Submersible pumps are a vital technology for a multitude of applications requiring fluid to be lifted from below the pump’s operating level. Their ability to operate efficiently while submerged, eliminating priming and cavitation concerns related to suction lift, makes them a reliable and effective solution. From providing clean drinking water from deep wells to managing wastewater and powering industrial processes, submersible pumps play a critical, often unseen, role in modern infrastructure and industry.