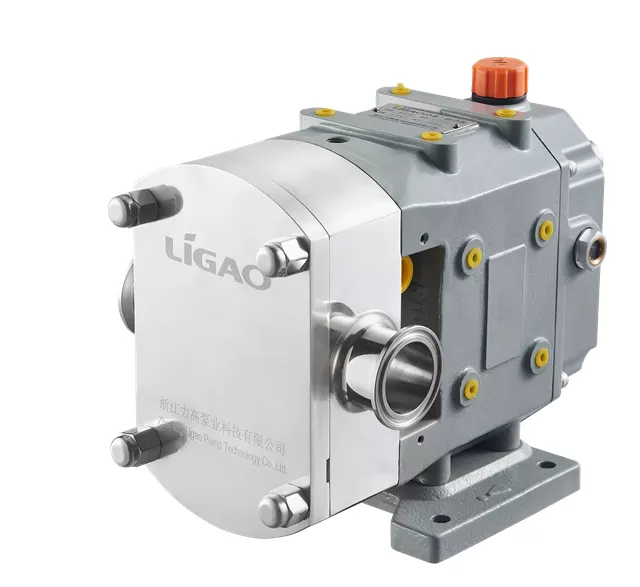
Rotary Lobe Pumps Explained
Gentle and Versatile Positive Displacement Pumping
Introduction to Rotary Lobe Pumps
Rotary lobe pumps are a type of positive displacement pump that use two or more intermeshing lobes rotating within a close-fitting pump casing to transfer fluids. They are known for their gentle pumping action, ability to handle solids, slurries, pastes, and a wide range of viscosities. The lobes do not typically make contact with each other, being driven by external timing gears, which minimizes wear and product degradation. This makes them highly suitable for sanitary, hygienic, and shear-sensitive applications.
Working Principle: Synchronized Rotation
The pumping action is achieved by counter-rotating lobes:
- Lobe Rotation & Suction: Two (or more) lobes rotate in opposite directions within the pump casing. As the lobes unmesh on the suction side, they create an expanding volume, reducing pressure and drawing fluid into the pump.
- Fluid Entrapment: Fluid is trapped in the pockets formed between the lobes and the pump casing.
- Transfer: The trapped fluid is carried around the periphery of the casing by the rotating lobes. The lobes do not pass fluid between them at the center.
- Discharge: As the lobes re-mesh on the discharge side, the volume of the pockets decreases, forcing the fluid out through the discharge port.
Timing gears outside the pumping chamber synchronize the lobe rotation, preventing contact and wear between the lobes.
Simplified Rotary Lobe Action
Key Components of a Rotary Lobe Pump
Lobes (Rotors)
The rotating elements that trap and move the fluid. Available in various profiles (bi-lobe, tri-lobe, multi-lobe, helical) to suit different applications.
Pump Casing (Housing)
The stationary body that encloses the lobes and forms the pumping chambers. Contains inlet and outlet ports.
Shafts
Support and drive the lobes. One is typically the drive shaft, the other(s) are driven via timing gears.
Bearings
Support the shafts, located outside the wetted area to prevent contamination.
Seals (Shaft Seals)
Prevent leakage along the shafts where they enter the pump casing. Mechanical seals or packing are common.
Timing Gears
Located in a separate gearbox, they synchronize the rotation of the lobes to ensure they do not contact each other.
Gearbox & Drive Motor
The gearbox (often integrated) reduces motor speed and increases torque. The motor provides the prime motive power.
Main Lobe Designs/Profiles
Bi-Lobe
Two lobes per rotor. Good for larger solids, more pulsation.
Tri-Lobe
Three lobes per rotor. Smoother flow than bi-lobe, handles smaller solids.
Multi-Lobe
Four or more lobes. Provides very smooth, low-pulsation flow, less solids handling.
Helical Lobes
Lobes have a twisted profile. Offer very low pulsation and gentle handling, good for high viscosity.
The choice of lobe profile depends on the fluid characteristics (viscosity, solids content, shear sensitivity) and desired flow characteristics (pulsation).
Advantages & Disadvantages
Advantages
- Gentle Pumping Action: Low shear, ideal for delicate or shear-sensitive fluids.
- Handles Solids & Slurries: Can pump fluids with entrained solids, particles, or large chunks (depending on lobe design).
- Handles Wide Viscosity Range: Effective for both thin and very thick liquids.
- Non-Contacting Lobes: Minimizes wear on pumping elements, allows for dry running for short periods (some designs).
- Hygienic Design: Easy to clean (CIP/SIP capabilities), suitable for food, beverage, and pharmaceutical applications.
- Self-Priming: Good suction lift capabilities.
- Reversible Flow: Can pump in either direction by reversing motor rotation.
- Constant Flow Rate: Delivers a predictable flow rate proportional to speed, relatively independent of pressure.
Disadvantages
- Larger footprint and heavier than some other pump types for the same capacity.
- Higher initial cost compared to simpler pumps like centrifugal or basic gear pumps.
- Requires timing gears, adding complexity and a potential maintenance point.
- Not ideal for very thin, non-lubricating liquids at high pressures due to internal slip.
- Can be sensitive to system overpressure if a relief valve is not installed.
- Flow can be pulsating, especially with fewer lobes (e.g., bi-lobe).
- Lower pressure capabilities compared to piston or screw pumps.
Common Materials of Construction
Pump Casing
- Stainless Steel (316L, 304L – common for sanitary)
- Ductile Iron
- Cast Iron
- Special Alloys (e.g., Hastelloy®, Duplex SS)
Lobes (Rotors)
- Stainless Steel (often hardened or coated)
- Elastomer-coated metal lobes (e.g., NBR, EPDM, Viton® for specific applications)
- Non-galling alloys (e.g., Alloy 88)
- Engineered Plastics
Shaft Seals
- Mechanical Seals (single, double, flushed)
- Lip Seals
- O-Ring Seals
- Component seals with various face materials (Carbon, SiC, TC) and elastomers.
Typical Applications
Rotary lobe pumps excel in applications requiring gentle handling and hygiene:
Key Selection Considerations
- Fluid Properties: Viscosity, shear sensitivity, presence and size of solids, abrasiveness, temperature, chemical compatibility.
- Hygiene Requirements: CIP/SIP capability, FDA/EHEDG/3-A standards.
- Flow Rate & Discharge Pressure.
- Lobe Profile & Number of Lobes: Based on fluid characteristics and pulsation tolerance.
- Materials of Construction: For wetted parts (casing, lobes, seals).
- Operating Speed: Lower speeds for higher viscosity or shear-sensitive fluids.
- NPSHa and Suction Conditions.
- Maintenance Needs: Ease of seal and lobe replacement.
- Drive and Gearbox Sizing.
- Cost (Initial and Total Cost of Ownership).
Rotary Lobe vs. Gear & Peristaltic Pumps
Feature | Rotary Lobe Pump | Gear Pump | Peristaltic Pump |
---|---|---|---|
Solids Handling | Good (soft solids, large particles) | Poor (abrasives cause wear) | Good (contained in tube) |
Shear Sensitivity | Very Low Shear (gentle) | Moderate to High Shear | Very Low Shear |
Hygienic Design | Excellent (CIP/SIP capable) | Limited (crevices) | Excellent (fluid in tube only) |
Dry Running | Limited (some designs better) | Poor | Good (limited by tube life) |
Cost | Moderate to High | Low to Moderate | Moderate (tube is consumable) |
Gentle Giants for Demanding Fluids
Rotary lobe pumps provide a robust and versatile solution for transferring a wide variety of fluids, especially those that are viscous, shear-sensitive, or contain solids. Their non-contacting lobe design and hygienic capabilities make them a preferred choice in industries like food & beverage, pharmaceuticals, and chemicals. While they may have a higher initial cost than some alternatives, their gentle handling, reliability, and ease of maintenance often result in a lower total cost of ownership for suitable applications.