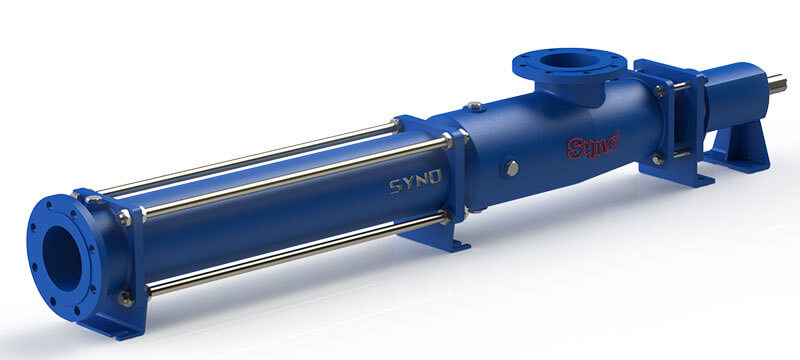
Progressive Cavity Pumps Explained
Handling Difficult Fluids with Unique Helical Action
Introduction to Progressive Cavity Pumps (PCPs)
Progressive Cavity Pumps (PCPs), also known as progressing cavity pumps or eccentric screw pumps, are a type of positive displacement pump. They are renowned for their ability to handle highly viscous, abrasive, shear-sensitive fluids, and those containing solids or entrained gases. Their unique design, featuring a helical rotor rotating eccentrically within a resilient helical stator, creates a series of sealed cavities that progress along the pump, gently conveying the fluid.
Working Principle: Progressing Helical Cavities
The pumping action is based on the interaction of a rotor and stator:
- Rotor & Stator Geometry: A single external helix metallic rotor rotates eccentrically inside a double internal helix elastomeric stator. The stator typically has twice the pitch length of the rotor.
- Cavity Formation: This geometry creates a series of sealed, lens-shaped cavities (pockets) between the rotor and stator.
- Eccentric Rotation: As the rotor turns, these cavities progress axially from the suction end to the discharge end of the pump.
- Fluid Conveyance: Fluid entering the suction port is trapped in these progressing cavities and is steadily and gently moved towards the discharge port without pulsation or high shear.
The volume of the cavities remains constant as they move, resulting in a predictable, positive displacement flow proportional to the pump’s speed.
Simplified Progressive Cavity Action
Key Components of a Progressive Cavity Pump
Rotor
A precision-machined single external helix, typically made of hardened steel, stainless steel, or coated for wear resistance.
Stator
A double internal helix, usually made of an elastomeric material (e.g., NBR, EPDM, Viton®) bonded inside a steel tube. Material choice is critical for fluid compatibility and temperature.
Drive Shaft & Connecting Rod/Universal Joint
Transmits power from the motor to the eccentrically rotating rotor. Universal joints or flexible connecting rods accommodate the eccentric motion.
Bearing Housing
Houses bearings that support the drive shaft and absorb axial and radial loads.
Shaft Seals
Prevent leakage along the drive shaft. Mechanical seals or gland packing are common.
Suction & Discharge Housing/Ports
Connect the pump to the system piping. Suction housing can be standard or an open hopper for very viscous materials.
Main Design Variations
Standard Industrial PCP
Most common configuration for a wide range of industrial applications, with flanged or threaded connections.
Open Hopper PCP
Features a large, open rectangular inlet hopper with an auger feed screw to assist highly viscous, non-flowing, or dewatered materials into the pumping elements.
Dosing/Metering PCP
Designed for precise, repeatable flow rates, often smaller in size and driven by variable speed motors for accurate chemical dosing.
Vertical PCP
Pump is mounted vertically, often for sump emptying, barrel unloading, or applications with limited horizontal space.
Variations also exist in the number of stages (rotor/stator length) to achieve different pressure capabilities.
Drive Methods
PCPs are typically driven by:
Electric Motors
Most common, often coupled with gear reducers to achieve optimal pump speed.
Geared Motors
Integrated motor and gearbox units for precise speed control.
Hydraulic Motors
Used in mobile applications or where hydraulic power is readily available.
Advantages & Disadvantages
Advantages
- Handles High Viscosities: Excellent for thick, pasty, and non-Newtonian fluids.
- Gentle Pumping Action: Very low shear, ideal for delicate, shear-sensitive products (e.g., food, polymers, live cultures).
- Handles Solids & Abrasives: Can pump fluids with significant solids content and abrasive particles with appropriate material selection.
- Pulsation-Free Flow: Delivers a smooth, continuous, and non-pulsating output.
- Self-Priming: Good suction lift capabilities, can often prime dry (depending on stator material).
- Accurate & Repeatable Flow: Flow rate is directly proportional to speed, making them suitable for metering.
- Reversible Flow Direction (by reversing motor rotation).
- Can Handle Entrained Gases and Multiphase Flows.
Disadvantages
- Stator Wear: The elastomeric stator is a primary wear part and requires periodic replacement, especially with abrasive fluids or high temperatures.
- Larger Footprint: Can be larger and heavier than other pump types for equivalent flow rates.
- Temperature Limitations: Elastomeric stator materials have temperature limits.
- Dry Running Limitations: While some can run dry for short periods, prolonged dry running will damage the stator.
- Pressure Limitations: Typically lower maximum pressure compared to some piston or high-pressure gear pumps.
- Higher Initial Cost: Can be more expensive than simpler pump designs.
- Requires careful material selection for rotor and stator based on fluid compatibility.
Common Materials of Construction
Rotor
- Hardened Tool Steel
- Stainless Steel (304, 316, Duplex)
- Chrome-Plated Steel
- Special Alloys (e.g., Hastelloy®)
Stator (Elastomer)
- NBR (Nitrile) – good for oils, fuels
- EPDM – good for water, some chemicals, good temperature range
- Viton® (FKM) – excellent chemical and temperature resistance
- Natural Rubber (NR) – good abrasion resistance
- Hypalon®, CSM – good chemical resistance
- PTFE (for specific applications, often in a rigid housing)
Casing/Housing
- Cast Iron, Ductile Iron
- Carbon Steel
- Stainless Steel
- Special Alloys
Typical Applications
PCPs are essential for handling challenging fluids across industries:
Key Selection Considerations
- Fluid Properties: Viscosity, solids content (size, concentration, abrasiveness), shear sensitivity, chemical compatibility, temperature.
- Flow Rate & Discharge Pressure Requirements.
- Stator Material Selection: Critical for fluid compatibility, temperature, and abrasion resistance.
- Rotor Material & Coating: For wear and corrosion resistance.
- Operating Speed: Lower speeds are generally better for viscous/abrasive fluids and longer stator life.
- NPSHa and Suction Conditions.
- Dry Running Potential: Some designs tolerate it better, but generally to be avoided.
- CIP/SIP Requirements (for hygienic applications).
- Space and Drive Configuration.
- Maintenance: Stator replacement is the main wear item.
PCP vs. Lobe & Screw Pumps (Brief)
Feature | Progressive Cavity Pump | Rotary Lobe Pump | Screw Pump (Multi-Screw) |
---|---|---|---|
Solids Handling | Excellent (can handle large solids, fibers) | Good (soft solids, some particles) | Limited (typically clean fluids) |
Shear Sensitivity | Very Low Shear | Very Low Shear | Low to Moderate Shear |
Pulsation | Very Low / None | Moderate (depends on lobe count) | Very Low / None |
Pressure Range | Moderate to High (staged designs) | Low to Moderate | Moderate to Very High |
Primary Wear Part | Stator (Elastomer) | Seals, Lobes (if contact occurs) | Screws, Casing (if abrasive) |
Unique Solutions for the Toughest Fluids
Progressive Cavity Pumps are uniquely equipped to handle fluids that other pump types struggle with, thanks to their gentle, low-shear pumping action and ability to convey highly viscous, abrasive, and solids-laden media. Their operational principle of progressing sealed cavities ensures a smooth, pulsation-free flow suitable for precise dosing and transferring delicate products. While stator wear is a key maintenance consideration, the overall versatility and problem-solving capabilities of PCPs make them indispensable in many challenging industrial applications.