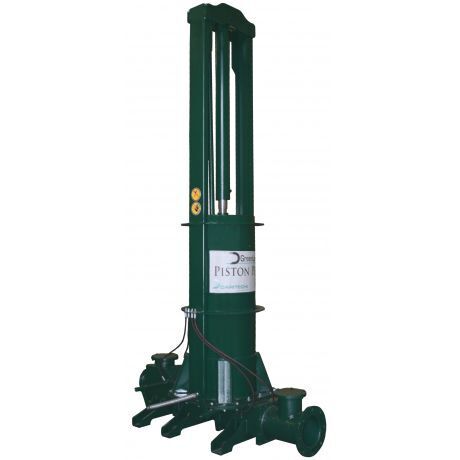
Piston Pumps Explained
Delivering High Pressure with Reciprocating Power
Introduction to Piston Pumps
Piston pumps are a type of positive displacement pump that use one or more reciprocating pistons (or plungers) to move fluid. They operate by drawing fluid into a cylinder during a suction stroke and then forcing it out under pressure during a discharge stroke. Piston pumps are known for their ability to generate high pressures, deliver precise flow rates (metering pumps), and handle a range of fluid viscosities. They are fundamental in many industrial, mobile, and high-pressure applications.
Working Principle: Reciprocating Action
The pumping cycle involves distinct strokes:
- Suction Stroke: The piston moves away from the inlet/outlet ports (e.g., downwards or backwards), increasing the volume within the cylinder. This creates a partial vacuum, causing the inlet valve to open and fluid to be drawn into the cylinder. The outlet valve remains closed due to higher downstream pressure or spring force.
- Discharge Stroke: The piston moves towards the inlet/outlet ports (e.g., upwards or forwards), decreasing the volume within the cylinder. This pressurizes the trapped fluid, forcing the inlet valve closed and the outlet valve open, expelling the fluid into the discharge line.
This cycle repeats, delivering a pulsating flow. Multiple pistons can be used to smooth out the flow and increase capacity.
SUCTION STROKE
DISCHARGE STROKE
Key Components of a Piston Pump
Piston (or Plunger)
The reciprocating component that directly displaces the fluid. Plungers are solid rods, pistons typically have seals.
Cylinder (or Block)
The chamber in which the piston reciprocates, containing the fluid during the pumping cycle.
Crankshaft / Cam Mechanism
Converts rotary motion from the prime mover into the reciprocating motion of the piston(s).
Connecting Rod
Links the crankshaft/cam to the piston.
Inlet & Outlet Valves
Check valves that control the direction of fluid flow into and out of the cylinder. Open and close automatically based on pressure differentials.
Seals (Piston Rings, Packing)
Prevent leakage past the piston/plunger and around the stem (if applicable).
Housing/Casing
The main body enclosing the pump components and providing mounting points and connections.
Main Types of Piston Pumps
Based on Piston Actuation:
Based on Piston Arrangement (Common in Hydraulics):
- Bent Axis Design: Cylinder block is at an angle to the driveshaft. Can be fixed or variable displacement. High efficiency and pressure.
- Swashplate Design (Inline): Pistons are driven by a rotating swashplate. Can be fixed or variable displacement (by changing swashplate angle). Common in mobile and industrial hydraulics.
Other Common Types:
Key Performance Parameters
- Displacement Volume (per stroke or per revolution): Volume of fluid displaced by one piston stroke or one revolution of the crankshaft/cam.
- Flow Rate (Q): Volume of fluid delivered per unit time (e.g., L/min, GPM). Proportional to speed and displacement.
- Pressure Rating: Maximum operating pressure the pump can generate or withstand.
- Speed (RPM or Strokes/min): Operating speed of the pump.
- Volumetric Efficiency (ηv): Ratio of actual flow to theoretical displacement (accounts for internal leakage/slip).
- Mechanical Efficiency (ηm): Accounts for friction losses.
- Overall Efficiency (ηo): ηv × ηm.
- NPSHr (Net Positive Suction Head Required): Minimum pressure at suction to prevent cavitation.
- Pulsation Level: Flow from single-piston pumps is pulsating; multiple pistons (duplex, triplex, etc.) reduce pulsation.
Advantages & Disadvantages
Advantages
- Can generate very high pressures.
- Deliver a precise and consistent flow rate (good for metering).
- Flow rate is relatively independent of discharge pressure.
- High volumetric efficiency, especially at high pressures.
- Can handle a range of fluid viscosities (depending on valve design).
- Self-priming capability (depending on design and condition).
- Variable displacement possible in some axial/radial designs for efficient power control.
Disadvantages
- Pulsating flow (especially single-piston designs), may require pulsation dampeners.
- More complex design with more moving parts than centrifugal or gear pumps.
- Higher initial cost compared to some other pump types.
- Can be noisy and generate vibrations.
- Valves and seals are subject to wear, especially with abrasive fluids.
- Generally larger and heavier for a given flow rate compared to centrifugal pumps.
- Requires a relief valve on the discharge side to prevent overpressure if flow is blocked.
Common Materials of Construction
Cylinder/Block & Housing
- Cast Iron, Ductile Iron
- Carbon Steel
- Stainless Steel (304, 316)
- Bronze
- Special Alloys for corrosive service
Piston/Plunger & Valves
- Hardened Steel
- Stainless Steel
- Ceramics (for plungers, high wear resistance)
- Bronze
- Engineered Plastics (for valve components)
Seals & Packing
- Elastomers (NBR, Viton®, EPDM)
- PTFE and other polymers
- Graphite packing
- Leather (for some hand pumps)
Typical Applications
Piston pumps are vital in applications requiring high pressure or precise flow:
Key Selection Considerations
- Required Discharge Pressure: Piston pumps excel at high pressures.
- Required Flow Rate and Precision: For metering or consistent delivery.
- Fluid Properties: Viscosity, corrosiveness, abrasiveness, temperature.
- Pulsation Tolerance: System may require dampeners for smoother flow.
- NPSHa vs. NPSHr: Important for preventing cavitation.
- Duty Cycle and Operating Speed.
- Material Compatibility with the fluid.
- Drive Type and Power Availability.
- Maintenance Requirements and Accessibility.
- Cost (Initial and Operating).
- Space and Noise Constraints.
Power and Precision with Reciprocating Action
Piston pumps are indispensable in applications demanding high pressures or precise, consistent flow rates. Their robust design and positive displacement principle allow them to overcome significant system resistance and accurately meter fluids. While they may introduce pulsation and can be more complex than some other pump types, their ability to deliver high performance in demanding conditions makes them a critical technology in hydraulic power, industrial cleaning, chemical dosing, and many other fields.