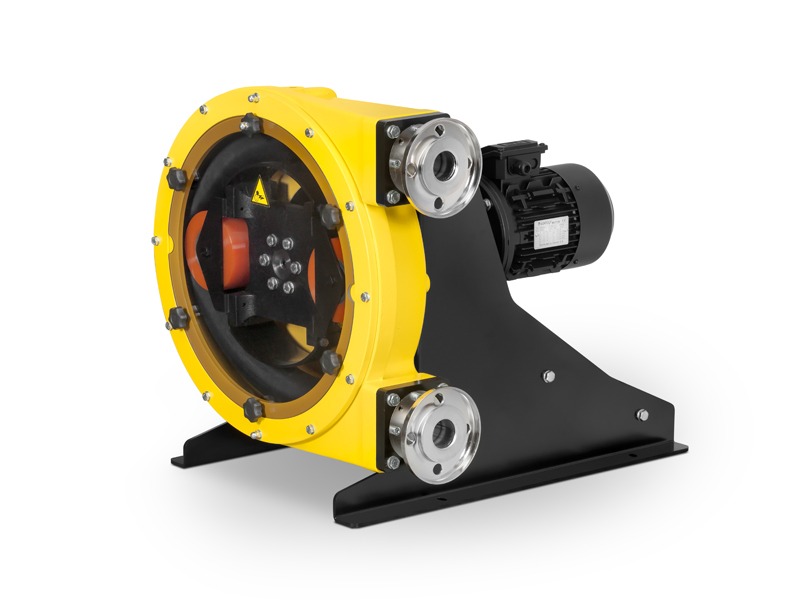
Peristaltic Pumps Explained
Gentle, Precise, and Contamination-Free Pumping
Introduction to Peristaltic Pumps
Peristaltic pumps, also known as roller pumps or hose pumps, are a type of positive displacement pump used for pumping a variety of fluids. Their unique operating principle involves compressing a flexible tube or hose with rotating rollers or shoes, creating a “peristaltic” wave that moves the fluid. A key advantage is that the pumped fluid is entirely contained within the tube/hose, preventing contamination of the fluid and the pump. This makes them ideal for hygienic, sterile, or aggressive fluids.
Working Principle: Squeezing Action
The pumping action is similar to how food moves through the intestines:
- Tube/Hose Placement: A flexible tube or reinforced hose is fitted inside a circular pump casing (track).
- Rotor with Rollers/Shoes: A rotor with multiple rollers, shoes, or wipers is mounted eccentrically or concentrically within the casing.
- Compression & Occlusion: As the rotor turns, the rollers/shoes progressively compress (occlude) the tube against the track. This creates a seal between the suction and discharge sides.
- Fluid Entrapment & Movement: The rotating action traps pockets of fluid between the rollers/shoes within the occluded section of the tube.
- Discharge: As the roller/shoe moves along the tube, it pushes the trapped fluid towards the discharge port. When the roller/shoe releases the tube, the tube recovers its shape, creating a vacuum that draws more fluid into the suction side.
Simplified Peristaltic Action
Key Components of a Peristaltic Pump
Flexible Tube or Hose
The only part in contact with the pumped fluid. Material selection is critical based on fluid compatibility, temperature, and pressure.
Rotor with Rollers or Shoes
The rotating assembly that compresses the tube/hose. Rollers provide lower friction; shoes can handle higher pressures (in hose pumps).
Pump Housing / Track / Casing
The rigid structure that supports the tube/hose and provides the surface against which it is compressed.
Motor / Drive Unit
Provides the rotational power to the rotor. Can be fixed or variable speed.
Bearings
Support the rotor shaft for smooth and efficient operation.
Inlet & Outlet Ports/Connectors
Points where the tube/hose connects to the system piping.
Main Types of Peristaltic Pumps
Tube Pumps (Roller Pumps)
Typically smaller, use flexible tubing, and operate at lower pressures and flow rates. Often have multiple rollers (2 to 8 or more) for smoother flow and reduced pulsation. Common in laboratory, medical, and dosing applications.
Hose Pumps (Shoe Pumps)
Larger, more robust design using reinforced hoses and often compressing shoes instead of rollers. Capable of higher pressures, higher flow rates, and handling more abrasive or viscous fluids. Common in industrial applications like wastewater, mining, and construction.
The number of rollers/shoes also influences performance: more rollers generally result in lower pulsation and more precise flow, but can reduce tube life due to more frequent compressions.
Drive Methods
Peristaltic pumps are typically driven by:
Electric Motors
AC, DC, stepper, or servo motors. Variable speed drives (VSDs/VFDs) are common for flow rate control.
Air Motors
Used in hazardous environments where electrical sparks are a concern.
Gearboxes
Often integrated to reduce motor speed and increase torque for the rotor.
Advantages & Disadvantages
Advantages
- Contamination-Free: Pumped fluid only contacts the inner surface of the tube/hose, ideal for sterile, hygienic, or aggressive fluids.
- Gentle Pumping Action: Low shear, suitable for shear-sensitive fluids (e.g., live cells, polymers, food products).
- Self-Priming: Excellent suction lift capabilities, can prime dry.
- Can Run Dry: For limited periods without damage (depends on tube/hose material and design).
- Reversible Flow: Direction of flow can often be reversed by changing rotor direction.
- Handles Solids and Viscous Fluids: Can pump fluids with high solids content or high viscosity (especially hose pumps).
- Accurate Dosing/Metering: Flow rate is proportional to rotor speed, enabling precise dosing.
- Easy Maintenance: Primary wear part is the tube/hose, which is relatively easy and inexpensive to replace.
Disadvantages
- Tube/Hose Wear: The tube/hose is a consumable part and requires periodic replacement due to fatigue from repeated compression.
- Pulsating Flow: Can produce a pulsating flow, especially with fewer rollers. Dampeners may be needed.
- Pressure Limitations: Generally lower pressure capabilities compared to other PD pumps (e.g., piston, gear). Hose pumps achieve higher pressures than tube pumps.
- Temperature Limitations: Limited by the temperature resistance of the tube/hose material.
- Flow Rate Limitations: Not typically used for very high flow rate applications compared to centrifugal pumps.
- Efficiency: Can be less energy efficient than some other pump types due to friction and tube deformation.
Common Materials
Tube / Hose Materials
- Silicone: Good for general purpose, medical, food grade, good flexibility.
- PVC (Polyvinyl Chloride): General purpose, good chemical resistance to some fluids.
- Viton® (FKM): Excellent chemical resistance, good for solvents, fuels, and oils.
- EPDM: Good for hot water, steam, some chemicals, good weather resistance.
- Santoprene® (TPV): Good chemical resistance, long life, often used in industrial applications.
- Norprene®: Long life, good for industrial and food applications.
- Natural Rubber (NR): For hose pumps, good abrasion resistance.
- Nitrile (NBR): Good for oils and fuels (hose pumps).
Pump Housing / Casing
- Engineering Plastics (e.g., ABS, Polycarbonate, Ryton® PPS)
- Aluminum
- Stainless Steel
- Painted Steel (for larger hose pumps)
Typical Applications
The unique features of peristaltic pumps make them ideal for specific tasks:
Key Selection Considerations
- Fluid Compatibility: Critical for tube/hose material selection.
- Flow Rate & Precision: Determines pump size, speed, and number of rollers.
- Discharge Pressure: Hose pumps for higher pressures, tube pumps for lower.
- Tubing/Hose Life Expectancy: Material, RPM, pressure, and occlusion setting impact life.
- Pulsation Tolerance: More rollers reduce pulsation. Dampeners may be needed.
- Suction Conditions: Peristaltic pumps have good lift, but this varies.
- Temperature of Fluid and Environment.
- Duty Cycle: Continuous or intermittent.
- Cleanliness/Sterility Requirements.
- Particle Size and Abrasiveness (if handling solids/slurries).
- Cost: Initial pump cost and ongoing cost of tube/hose replacement.
Peristaltic vs. Diaphragm & Gear Pumps
Feature | Peristaltic Pump | Diaphragm Pump (AODD) | Gear Pump |
---|---|---|---|
Fluid Contact | Only Tube/Hose | Diaphragms, Valves, Body | Gears, Casing, Seals |
Shear Sensitivity | Very Low Shear | Low to Moderate Shear | Moderate to High Shear |
Dry Running | Good (limited by tube) | Excellent | Poor |
Pulsation | Moderate (can be reduced) | High (dampeners often used) | Low |
Maintenance Focus | Tube/Hose Replacement | Diaphragms, Check Valves | Gears, Seals, Bearings |
Gentle, Precise, and Contamination-Free Pumping
Peristaltic pumps offer a unique set of advantages, particularly their ability to pump fluids without contamination and with very low shear. This makes them indispensable in hygienic applications, for handling sensitive or aggressive chemicals, and for precise dosing. While tube or hose life is a key operational consideration, their simplicity of maintenance and reliable performance in specific niches solidify their importance in modern fluid handling.