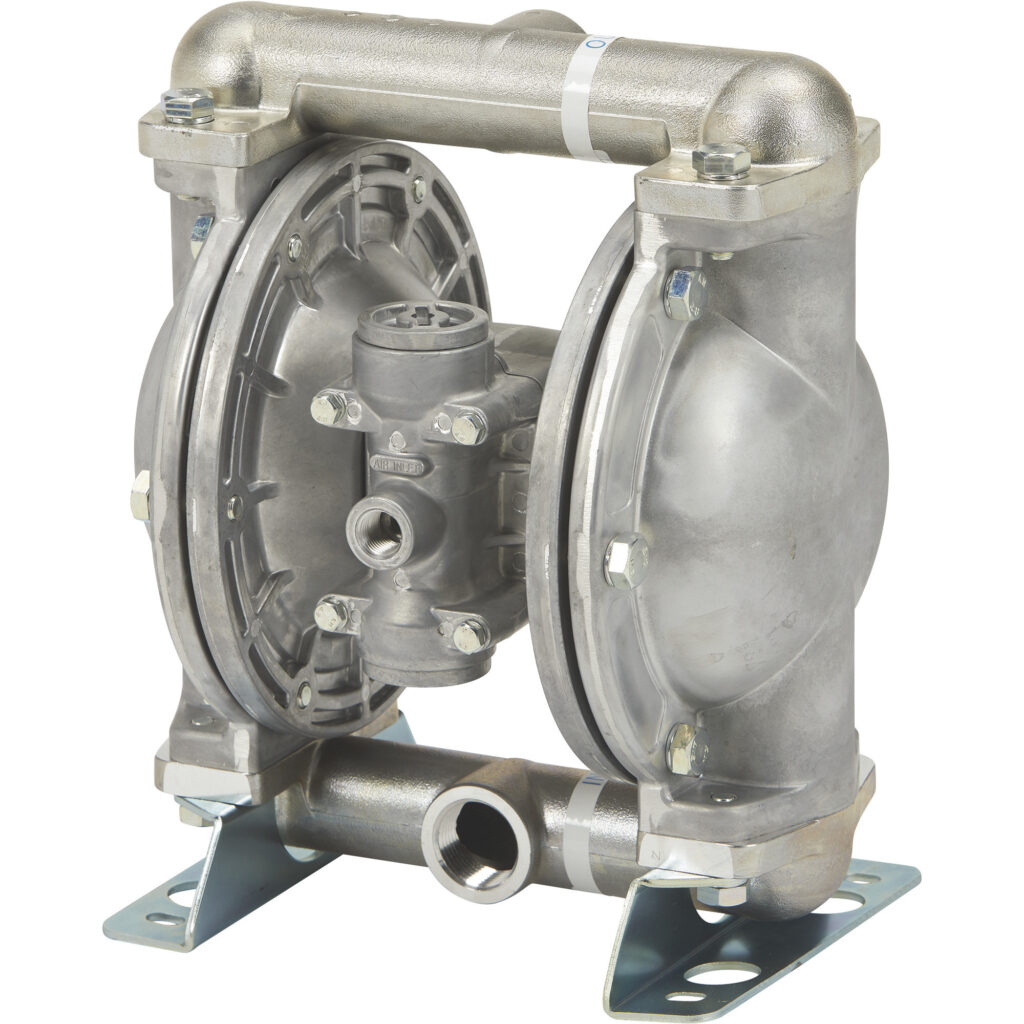
Diaphragm Pumps Explained
Versatile Solutions for Difficult Fluids and Dosing
Introduction to Diaphragm Pumps
Diaphragm pumps are a type of positive displacement pump that use a reciprocating flexible diaphragm in conjunction with check valves (inlet and outlet) to pump fluids. The diaphragm acts as a separating membrane between the drive mechanism and the fluid, making them ideal for handling corrosive, abrasive, viscous, or shear-sensitive fluids, as well as for applications requiring leak-free operation. They are widely used across many industries due to their versatility and ability to handle a diverse range of materials.
Working Principle: Flexing for Flow
The pumping cycle involves the flexing of one or more diaphragms:
- Suction Stroke: The diaphragm moves away from the pump chamber (e.g., pulled back by a mechanical linkage or pushed by air pressure on its non-wetted side in AODD pumps). This increases the volume of the pumping chamber, reducing its pressure. The inlet check valve opens, and fluid is drawn into the chamber. The outlet check valve remains closed.
- Discharge Stroke: The diaphragm moves towards the pump chamber (e.g., pushed forward or by air pressure), decreasing the chamber volume. This pressurizes the trapped fluid, forcing the inlet check valve to close and the outlet check valve to open, expelling fluid into the discharge line.
This cycle repeats. Air-Operated Double Diaphragm (AODD) pumps use two diaphragms connected by a shaft, with air pressure alternating between them to create continuous (though pulsating) flow.
SUCTION STROKE
DISCHARGE STROKE
Key Components of a Diaphragm Pump
Diaphragm(s)
The flexible membrane(s) that isolates the fluid from the drive mechanism and creates the pumping action. Material selection is critical.
Pump Chamber(s) / Fluid Housing
The cavity where the fluid is drawn into and expelled from by the diaphragm’s movement.
Inlet & Outlet Check Valves
Ball, flap, or poppet type check valves that control the direction of fluid flow into and out of the pump chamber(s).
Drive Mechanism
The means by which the diaphragm is reciprocated (e.g., air distribution valve and pilot valve for AODD, mechanical linkage for mechanically driven, hydraulic fluid for hydraulically driven).
Pump Body/Housing
The main structure enclosing all components and providing connections.
Air Valve / Air Motor (AODD)
Controls the alternating supply of compressed air to the air chambers behind the diaphragms in an AODD pump.
Main Types of Diaphragm Pumps
Air-Operated Double Diaphragm (AODD) Pump
Most common industrial type. Uses compressed air acting on two flexible diaphragms linked by a common shaft. One diaphragm performs suction while the other discharges, then they alternate. Robust, self-priming, can run dry.
Mechanically Actuated Diaphragm Pump
Diaphragm is moved by a mechanical linkage (e.g., crank, cam) connected to an electric motor or engine. Often used for metering or dosing due to consistent stroke length.
Hydraulically Actuated Diaphragm Pump
Hydraulic fluid acts on one side of the diaphragm, while the process fluid is on the other. The diaphragm isolates the process fluid from the hydraulic system. Used for high pressures and accurate metering.
Key Performance Parameters
- Flow Rate (Capacity): Volume of fluid pumped per unit time (e.g., GPM, L/min).
- Discharge Pressure (Head): Maximum pressure the pump can generate.
- Suction Lift Capability: Ability to draw fluid from a level below the pump.
- Air Consumption & Air Pressure (for AODD): Critical for AODD pump sizing and operation.
- Material Compatibility: Diaphragms, check valves, and wetted body parts with the pumped fluid.
- Solids Handling Capability: Maximum particle size the pump can pass.
- Viscosity Handling: Maximum fluid viscosity the pump can handle efficiently.
- Temperature Limits: Dictated by diaphragm and body materials.
- Cycle Rate / Strokes per Minute.
Advantages & Disadvantages
Advantages
- Excellent Chemical Resistance: Wide range of diaphragm and body materials.
- Handles Abrasives & Slurries: Fluid path is often smooth, check valves can be robust.
- Self-Priming: Good suction lift capabilities.
- Can Run Dry: AODD pumps can typically run dry for extended periods without damage.
- Shear-Sensitive Handling: Gentle pumping action for delicate fluids.
- Leak-Free Operation (Sealless Design): No dynamic seals on the process fluid side.
- Variable Flow & Pressure (AODD): Easily controlled by regulating air supply.
- Portable and Simple to Operate (AODD).
- Can handle entrained air/gases.
Disadvantages
- Pulsating Flow: May require pulsation dampeners for smooth discharge.
- Limited Pressure Capability: Generally lower than piston or gear pumps (AODD limited by air pressure).
- Air Consumption (AODD): Can be significant, impacting energy costs if compressed air is expensive.
- Diaphragm Wear: Diaphragms are wear parts and require periodic replacement.
- Noise Levels (AODD): Air exhaust can be noisy; mufflers are often used.
- Efficiency: Can be lower than some other pump types, especially AODD.
- Temperature Limitations: Dictated by diaphragm and valve materials.
Common Materials of Construction
Pump Body (Wetted Parts)
- Polypropylene (PP)
- PVDF (Kynar®)
- Stainless Steel (316, 304)
- Aluminum
- Cast Iron / Ductile Iron
- Acetal
Diaphragms
- PTFE (Teflon®) – excellent chemical resistance
- Santoprene® (TPV) – good general purpose, flex life
- Nitrile (Buna-N) – oils, fuels
- EPDM – caustics, some acids, hot water
- Viton® (FKM) – solvents, aggressive chemicals, high temp
- Hytrel® – good flex life, abrasion resistance
Check Valves (Balls/Seats)
- PTFE
- Stainless Steel
- Santoprene®, Nitrile, EPDM, Viton® (for balls/flaps)
- Hastelloy®, Alloy C
Typical Applications
Diaphragm pumps are workhorses in diverse industries:
Key Selection Considerations
- Fluid Compatibility: Critical for diaphragm, valve, and body material selection. Check chemical resistance charts.
- Flow Rate & Discharge Pressure Requirements.
- Viscosity and Solids Content of the fluid.
- Temperature of the fluid and environment.
- Suction Conditions (Lift or Flooded Suction).
- Air Supply Availability & Cost (for AODD pumps).
- Duty Cycle (Continuous or Intermittent).
- Pulsation Sensitivity of the System.
- Space Limitations and Portability Needs.
- Certifications Required (e.g., FDA, ATEX).
- Maintenance: Diaphragm life and ease of replacement.
Versatile Pumping for Challenging Fluids
Diaphragm pumps, particularly AODD pumps, offer a robust and versatile solution for handling a wide spectrum of fluids, including those that are corrosive, abrasive, viscous, or shear-sensitive. Their sealless design, ability to run dry, and self-priming capabilities make them invaluable in many demanding industrial environments. While they have limitations in terms of pressure and flow pulsation, careful selection based on application specifics ensures reliable and effective fluid transfer.