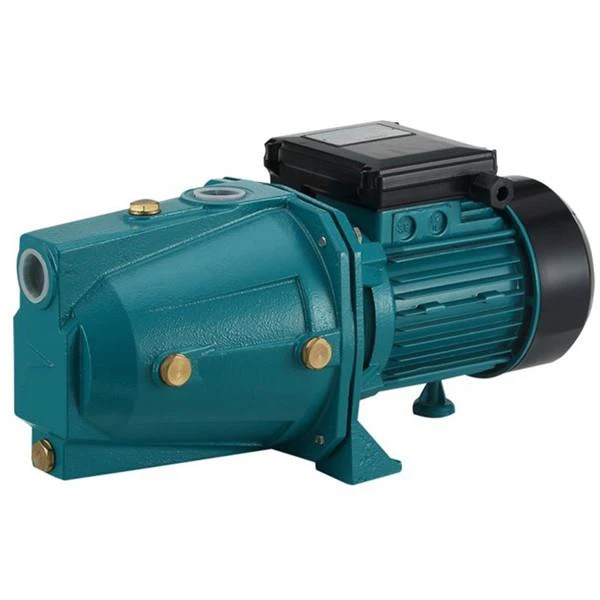
Jet Pumps Explained
Harnessing Fluid Dynamics for Pumping & Vacuum
Introduction to Jet Pumps
Jet pumps, also known as ejectors or eductors, are a unique type of pump that have no traditional moving parts like impellers or pistons. They operate based on the Venturi principle and momentum transfer, using a high-velocity jet of one fluid (the “motive” fluid) to entrain, mix with, and move a second fluid (the “suction” or “entrained” fluid). These devices are valued for their simplicity, reliability, and ability to handle corrosive, abrasive, or hazardous fluids, as well as for creating vacuum.
Working Principle: Venturi Effect & Momentum Transfer
The operation involves several key stages:
- Motive Fluid Acceleration: A high-pressure motive fluid (liquid, steam, or gas) is passed through a converging nozzle, increasing its velocity and converting pressure energy into kinetic energy.
- Low-Pressure Zone Creation: As the high-velocity motive fluid exits the nozzle into the suction chamber, its pressure drops significantly (Venturi effect), creating a low-pressure zone.
- Entrainment of Suction Fluid: This low pressure draws the secondary (suction) fluid into the suction chamber.
- Mixing: The motive and suction fluids mix in the mixing tube or throat, where momentum is transferred from the high-velocity motive fluid to the combined stream.
- Pressure Recovery: The mixed stream then passes through a diverging section called a diffuser, where its velocity decreases and kinetic energy is converted back into pressure energy, discharging the combined fluid at a pressure higher than the suction pressure but lower than the motive fluid pressure.
Simplified Jet Pump Operation
Key Components of a Jet Pump
Nozzle (Primary Nozzle)
A converging section that accelerates the motive fluid to high velocity.
Suction Chamber
The area where the motive fluid jet creates low pressure, drawing in the suction fluid.
Mixing Tube / Throat
A typically straight section where the motive and suction fluids mix and momentum exchange occurs.
Diffuser
A diverging section that slows down the mixed fluid, converting kinetic energy back into pressure energy.
Body / Housing
The main structure containing all components and providing connections.
Inlets & Outlet
Ports for motive fluid supply, suction fluid intake, and combined fluid discharge.
Main Types/Names of Jet Pumps
While the principle is similar, jet pumps are often named based on their motive fluid or primary application:
Ejectors
General term. Often refers to steam-jet ejectors (steam as motive fluid to create vacuum or pump gases) or air ejectors.
Eductors
Typically use a liquid (e.g., water) as the motive fluid to pump or mix other liquids, slurries, or granular solids.
Injectors
A specific type of jet pump historically used to feed water into steam boilers, using steam as the motive fluid.
Aspirators
Often refers to devices using a gas (like air from a tap attachment) or liquid to create a moderate vacuum for laboratory or small-scale suction tasks.
Common Motive Fluids
Steam
High energy, widely used for creating deep vacuums (steam-jet ejectors).
Water/Liquids
Common for eductors, pumping liquids/slurries, or creating moderate vacuum.
Air/Gases
Used in air ejectors or aspirators for vacuum or pumping gases.
Advantages & Disadvantages
Advantages
- No moving parts in the pumping section: High reliability, low maintenance.
- Simple and robust construction.
- Can handle corrosive, abrasive, hazardous, or high-temperature fluids (material dependent).
- Can create high vacuum levels (multi-stage steam ejectors).
- Relatively low initial cost for certain applications.
- Self-priming for entraining liquids.
- Can handle solids or slurries (eductors).
- Tolerant of harsh operating conditions.
Disadvantages
- Relatively low energy efficiency compared to mechanical pumps.
- Requires a separate source of high-pressure motive fluid.
- Motive fluid consumption can be significant, impacting operating costs.
- Performance is sensitive to variations in motive and suction pressures.
- Discharge fluid is a mixture of motive and suction fluids (may require separation).
- Limited turndown ratio (range of efficient operation).
- Can be noisy, especially steam ejectors.
Common Materials of Construction
Materials are chosen based on fluid compatibility, temperature, and pressure.
Typical Applications
Jet pumps are found in diverse industrial and scientific fields:
Key Performance & Selection Considerations
- Motive Fluid: Availability, pressure, temperature, cost.
- Suction Fluid: Properties (density, viscosity, corrosivity), required flow rate, suction pressure/lift.
- Discharge Conditions: Required discharge pressure and capacity.
- Entrainment Ratio (Mass or Volume): Ratio of suction fluid flow to motive fluid flow. A key performance indicator.
- Compression Ratio: Ratio of discharge pressure to suction pressure.
- Material Compatibility: With both motive and suction fluids.
- Efficiency: Jet pumps are generally less efficient than mechanical pumps, so motive fluid consumption is a major factor.
- NPSH (for liquid eductors): Net Positive Suction Head available at the suction inlet.
- Operating Environment: Space, temperature, hazardous area classification.
- Need for Multi-staging: To achieve higher vacuum or compression ratios.
Jet Pump vs. Mechanical Pumps (Brief)
Feature | Jet Pump | Mechanical Pump (e.g., Centrifugal/PD) |
---|---|---|
Moving Parts (Pumping Section) | None | Yes (Impeller, Gears, Pistons, etc.) |
Maintenance | Very Low | Higher (Seals, Bearings, Wear Parts) |
Energy Efficiency | Generally Lower | Generally Higher |
Handling Harsh Fluids | Excellent (Material Dependent) | Varies, can be challenging/costly |
Initial Cost | Can be Lower (for specific duties) | Varies widely |
Simplicity in Motion: The Power of Jet Pumps
Jet pumps, through their ingenious use of fluid dynamics, offer a simple, robust, and often cost-effective solution for pumping, mixing, and creating vacuum in a wide range of challenging environments. Their lack of moving parts in the flow path makes them exceptionally reliable and low-maintenance, especially when dealing with difficult fluids. While their energy efficiency might be lower than mechanical alternatives, their unique advantages make them indispensable for many critical industrial and scientific applications.