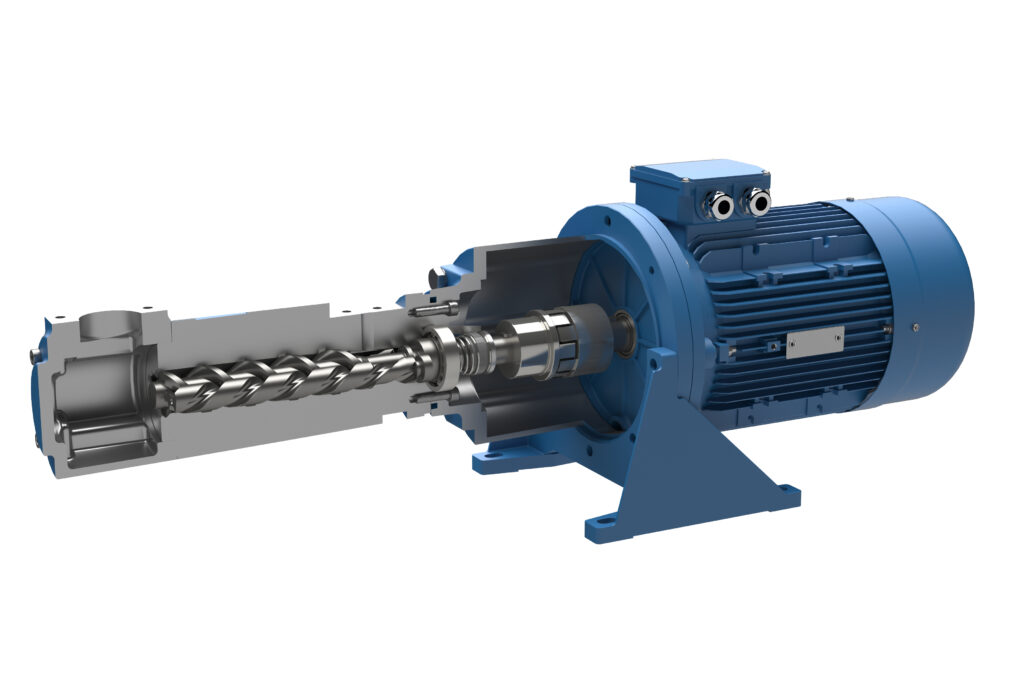
Screw Pumps Explained
Versatile Positive Displacement for Demanding Fluids
Introduction to Screw Pumps
Screw pumps are a type of rotary positive displacement pump that use one or more intermeshing screws to move fluids or solids along the screw(s) axis. As the screws rotate, they trap fluid in cavities between the screw threads and the pump housing, conveying it axially from suction to discharge. They are known for their ability to handle a wide range of fluid viscosities, multiphase flows, shear-sensitive materials, and even some solids, providing a smooth, pulsation-free flow.
Working Principle: Axial Fluid Conveyance
The operation relies on the geometry of rotating screws:
- Screw Rotation: One or more screws (driver screw and often idler screws) rotate within a close-fitting housing or liner.
- Cavity Formation: As the screws rotate, they create sealed cavities between the screw threads (flights) and the housing. These cavities progress axially along the screws.
- Fluid Entrapment & Transfer: Fluid enters the suction port and is trapped within these advancing cavities.
- Axial Displacement: The rotation of the screws pushes these fluid-filled cavities towards the discharge port, resulting in a continuous, non-pulsating flow.
The tight clearances between the screws and between the screws and the housing are critical for efficiency and preventing internal slip.
Simplified Twin Screw Action
Key Components of a Screw Pump
Screws (Rotors)
The primary pumping elements. Can be one (progressive cavity) or multiple (two, three, or more) intermeshing screws with precisely machined profiles.
Housing / Casing / Stator
The stationary body that encloses the screws and forms the outer boundary of the pumping cavities. In progressive cavity pumps, this is often an elastomeric stator.
Shafts
Support and drive the screws. The drive screw is connected to the motor.
Bearings
Support the shafts and withstand axial and radial loads. Can be internal (lubricated by pumped fluid) or external.
Seals
Prevent leakage along the drive shaft(s). Mechanical seals or packing are common.
Timing Gears (for some types)
Used in some multi-screw pumps (e.g., timed twin-screw) to synchronize the rotation of non-contacting screws, preventing metal-to-metal contact.
Inlet & Outlet Ports
Connections for the suction and discharge piping, typically aligned with the screw axis.
Main Types of Screw Pumps
Single Screw Pump (Progressive Cavity Pump – PCP)
Features a single helical rotor rotating eccentrically within a flexible, helical elastomeric stator. Creates progressing cavities. Excellent for viscous, abrasive, and shear-sensitive fluids, and solids handling.
Twin Screw Pump (Two-Screw)
Two intermeshing screws rotate in opposite directions. Can be timed (screws don’t touch, driven by timing gears) or untimed (screws drive each other, some contact). Good for high viscosity, multiphase, and shear-sensitive fluids. Self-priming.
Three Screw Pump
A central drive screw meshes with two idler screws. Forms sealed cavities that move fluid axially. Known for smooth, pulsation-free flow, high pressure capability, and handling lubricating oils and fuels.
Drive Methods
Screw pumps are typically driven by:
Electric Motors
Most common, often coupled directly or via a gearbox for speed reduction.
Engines (ICE)
For mobile or remote applications.
Gear Reducers
Often used to match motor speed to optimal pump speed, especially for viscous fluids.
Advantages & Disadvantages
Advantages
- Can handle a wide range of fluid viscosities, from thin to very thick.
- Excellent for shear-sensitive fluids due to gentle pumping action.
- Provide a smooth, pulsation-free flow.
- Good self-priming capabilities.
- Can handle fluids with entrained gas and multiphase flows.
- Some designs can handle solids and abrasives (e.g., PCPs).
- High pressure capabilities (especially three-screw pumps).
- Bi-directional flow possible for some types.
Disadvantages
- Generally larger and heavier than centrifugal pumps for the same flow rate.
- Can be more expensive initially compared to simpler pump types.
- Close internal clearances make them sensitive to hard solids or large particulates (except specialized PCP designs).
- Performance can be affected by wear on screws and housing/stator.
- Elastomeric stators in PCPs have temperature and chemical limitations and wear over time.
- Some types (timed multi-screw) require precise timing gears, adding complexity.
Common Materials of Construction
Housing/Casing/Stator
- Cast Iron, Ductile Iron
- Carbon Steel
- Stainless Steel (316, Duplex)
- Alloy Steels
- Elastomers (for PCP stators: NBR, EPDM, Viton®)
Screws/Rotors
- Hardened Tool Steels
- Stainless Steel (often hardened or coated)
- Alloy Steels
- Chrome-plated Steel
Shafts & Seals
- Shafts: Alloy Steel, Stainless Steel.
- Seals: Mechanical Seals (various face/elastomer combinations), Gland Packing.
Typical Applications
Screw pumps are highly versatile for demanding fluid handling:
Key Selection Considerations
- Fluid Properties: Crucially viscosity, but also lubricity, temperature, corrosiveness, abrasiveness, presence of solids or gas.
- Flow Rate & Pressure: Determine the pump size and type (single vs. multi-screw).
- NPSHa: Important for all pumps, including screw pumps.
- Shear Sensitivity: Screw pumps are generally good for shear-sensitive fluids.
- Material Compatibility: With fluid and operating environment.
- Operating Speed: Lower speeds for higher viscosities or abrasive fluids.
- System Protection: Relief valve is essential on the discharge side for PD pumps.
- Space & Mounting Configuration.
- Maintenance Requirements: PCP stators are wear items; timed gears require alignment.
- Cost (Initial and Lifecycle).
Screw Pump vs. Gear & Lobe Pumps
Feature | Screw Pump | Gear Pump | Lobe Pump |
---|---|---|---|
Pulsation | Very Low / None | Low to Moderate | Moderate |
Viscosity Range | Very Wide (Low to Extremely High) | Wide (Medium to High Best) | Wide (Medium to High Best) |
Solids Handling | Good (PCPs excellent, others limited) | Poor | Good (gentle) |
Shear Sensitivity | Very Good (Low Shear) | Moderate | Very Good (Low Shear) |
Pressure Capability | Moderate to Very High | Moderate to High | Low to Moderate |
Versatile Solutions for Complex Fluids
Screw pumps are highly versatile positive displacement pumps capable of handling a wide array of challenging fluids, from highly viscous liquids and multiphase flows to shear-sensitive and abrasive media. Their ability to provide a smooth, pulsation-free flow makes them ideal for applications requiring precise and gentle fluid transfer. While generally more complex and potentially costlier than simpler PD pumps, their unique capabilities often make them the optimal choice for demanding industrial processes.