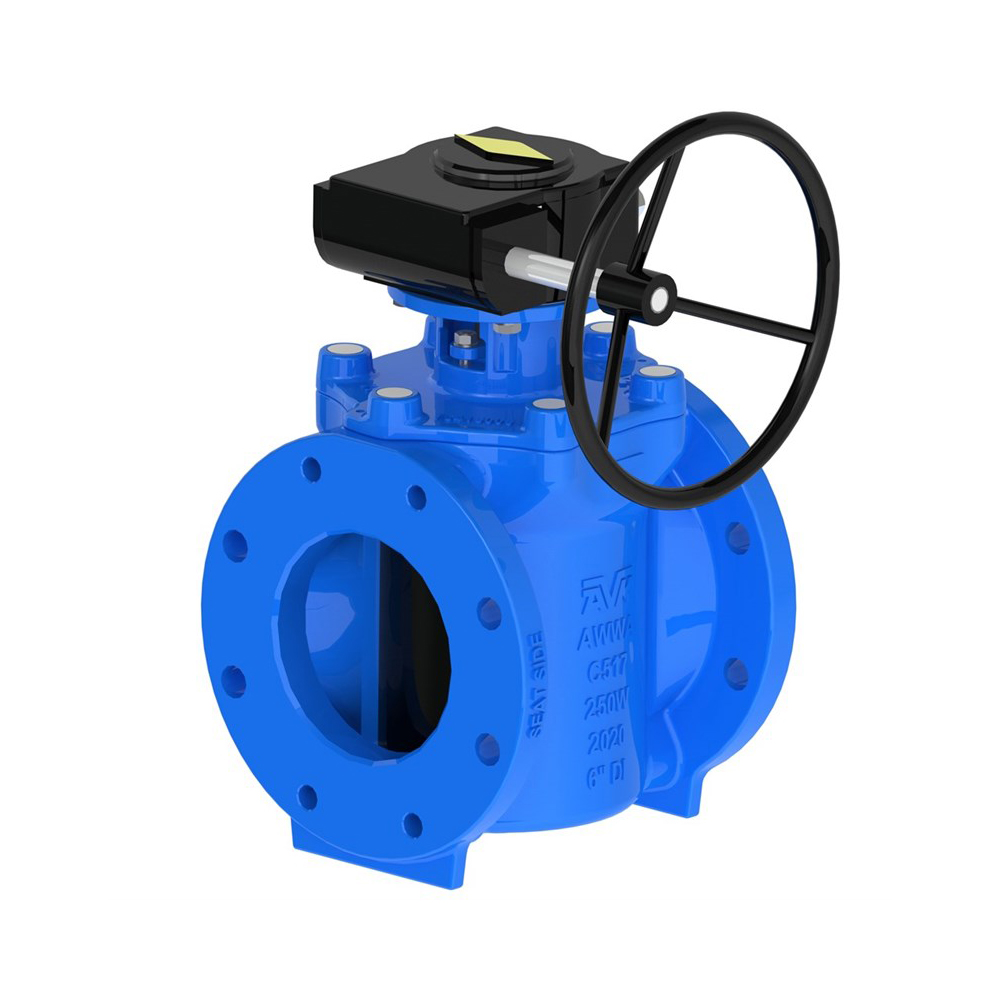
Plug Valves Explained
Understanding Design, Types, and Applications
Introduction to Plug Valves
Plug valves are quarter-turn rotational motion valves that use a tapered or cylindrical plug to stop or start flow. The plug has one or more hollow passageways (ports) going sideways through it. They are one of the oldest valve designs and are valued for their simple construction, tight shutoff, and quick operation. Plug valves are suitable for on/off isolation and, in some designs (multiport), for diverting flow.
Working Principle: Rotating Plug Control
The operation is straightforward:
- Quarter-Turn Operation: A 90-degree turn of the handle or actuator rotates the plug within the valve body.
- Port Alignment:
- When the plug’s port is aligned with the inlet and outlet ports of the valve body, the valve is OPEN, allowing flow.
- When the plug is rotated 90 degrees, the solid part of the plug blocks the flow path, and the valve is CLOSED.
- Sealing: In non-lubricated plug valves, a resilient sleeve or liner between the plug and body provides the seal. In lubricated types, a sealant injected between the plug and body creates the seal and reduces friction.
OPEN
CLOSED
Key Components of a Plug Valve
Valve Body
The main pressure-containing structure with a cavity for the plug and end connections.
Plug
The cylindrical or tapered closure element with one or more ports that rotates to control flow.
Stem
Connects the actuator/handle to the plug, transmitting the rotational torque.
Bonnet / Cover
Encloses the top of the valve and supports the stem and packing. Some designs are bonnetless.
Sleeve / Liner (Non-lubricated)
A resilient sleeve (e.g., PTFE) or lining within the body that seals against the plug and reduces friction.
Actuator/Handle
Mechanism for operating the valve (lever, wrench, gear operator, or automated actuator).
Packing / Seals
Prevent leakage around the stem and, in some designs, provide sealing for the plug or bonnet.
Main Types of Plug Valves
Based on Lubrication:
Based on Port Pattern:
Based on Plug Design:
Multiport Designs:
Actuation Methods
Plug valves are typically quarter-turn operated:
Manual (Wrench/Lever)
Common for smaller sizes, providing quick operation.
Manual (Gear Operator)
Reduces operating torque for larger or higher-pressure valves.
Pneumatic Actuator
Uses compressed air for automated, fast-acting operation.
Electric Actuator
Uses an electric motor for precise, automated control, suitable for remote locations.
Advantages & Disadvantages
Advantages
- Simple design with few moving parts.
- Quick quarter-turn on-off operation.
- Durable and provides tight shutoff, especially non-lubricated sleeved types.
- Can handle slurries and liquids with suspended solids (depending on design).
- Relatively low operating torque for non-lubricated types.
- Can be used for diverting services (multiport designs).
- In-line maintenance possible for some designs (e.g., top entry).
Disadvantages
- Higher operating torque than ball valves of similar size/pressure.
- Lubricated types require periodic re-lubrication to maintain seal and prevent sticking.
- Not ideal for throttling, though some designs (e.g., diamond port) offer limited capability.
- Tapered plugs can sometimes jam if not operated regularly or if there are significant temperature changes.
- Larger sizes can be bulky and heavy.
- Potential for high friction in some designs without proper lubrication or sleeve.
Common Materials of Construction
Valve Body
- Cast Iron, Ductile Iron
- Carbon Steel (A216 WCB, A105)
- Stainless Steel (A351 CF8M/316, CF8/304)
- Alloy Steels (Monel, Hastelloy, Alloy 20)
- Bronze, Brass
Plug
- Cast Iron (often coated)
- Carbon Steel (often plated or coated)
- Stainless Steel
- Alloy Steels
- PTFE or other polymer encapsulated plugs
Sleeve/Liner (Non-lubricated)
- PTFE (Teflon®) – most common
- Reinforced PTFE (RPTFE)
- PFA (Perfluoroalkoxy)
- UHMWPE (Ultra-High Molecular Weight Polyethylene)
Typical Applications
Plug valves are well-suited for a variety of services:
Key Selection Considerations
- Fluid Properties: Viscosity, abrasiveness, presence of solids, corrosiveness.
- Operating Pressure & Temperature: Determines material and valve type (lubricated vs. non-lubricated).
- Shutoff Requirements: Bubble-tight shutoff is achievable.
- Frequency of Operation: Quick operation is an advantage.
- Maintenance: Lubricated types require regular sealant injection; non-lubricated sleeves can wear.
- Port Type: Full bore for low pressure drop, rectangular for general use, multiport for diverting.
- Material Compatibility: Critical for body, plug, and sleeve/liner.
- Operating Torque: Can be higher than ball valves, may necessitate gear operators.
- Industry Standards: API 6D, API 599, ASME B16.34.
Plug Valve vs. Ball Valve (Brief Comparison)
Feature | Plug Valve | Ball Valve |
---|---|---|
Sealing Mechanism | Plug against body/sleeve (wedge action) or lubricant film | Ball against seats (compression) |
Cavity | Typically no major body cavity for fluid entrapment | Body cavity can trap fluid |
Operating Torque | Generally higher, especially lubricated types | Generally lower |
Slurry Handling | Often better, especially with specific port designs | Can handle some, but seats may wear |
Maintenance (Non-lubricated) | Sleeve replacement | Seat/seal replacement |
Simple, Robust, and Reliable Flow Control
Plug valves, with their long history and straightforward design, continue to be a reliable choice for on/off isolation and diverting services in many industries. Their ability to handle slurries and provide tight shutoff, especially in non-lubricated sleeved designs, makes them suitable for demanding applications. While they may have higher operating torques than some alternatives, their durability and simplicity often make them a cost-effective and dependable solution.